OpenVPX (Open Vertical Express) is an open-standard, high-performance modular architecture primarily used in military, aerospace, and industrial systems. It defines the framework for system-level integration of computing, storage, and networking components in a ruggedized chassis. OpenVPX enclosures house advanced, high-speed processing modules and ensure secure, reliable operation in harsh environments. These chassis are designed to meet stringent military and industrial standards for durability, thermal management, and electromagnetic shielding, offering customizable configurations for mission-critical applications. OpenVPX systems are ideal for applications where performance, scalability, and long-term reliability are essential.
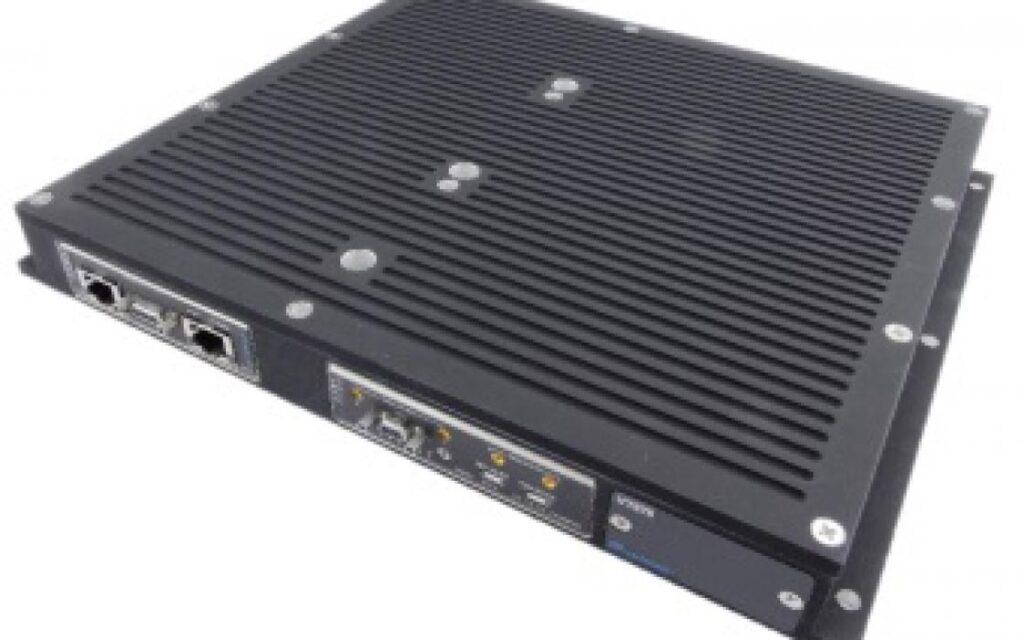
Ruggedized Design for Extreme Conditions
Designing a ruggedized OpenVPX chassis requires careful consideration of various harsh environmental factors such as shock, vibration, extreme temperatures, and exposure to dust, moisture, and chemicals. The chassis must be capable of protecting sensitive electronics while maintaining optimal performance under these demanding conditions. For military and aerospace applications, ensuring the system can endure tactical operations and function in the most hostile environments is critical. The rugged design must incorporate shock isolation, vibration resistance, and reliable heat dissipation to protect the internal components, often with little margin for error.
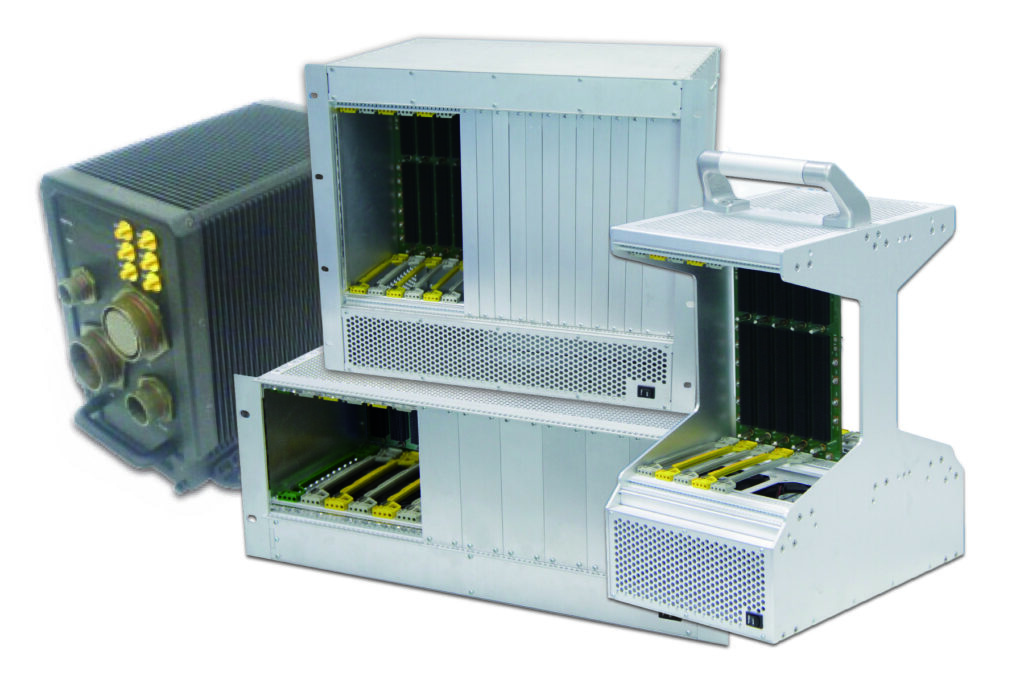
Compact, Secure, and TEMPEST-Compliant Solutions
The challenge of creating compact enclosures while ensuring they meet all security standards is another key difficulty. Space constraints often require efficient layout designs that maximize internal space while housing a complex array of components. Moreover, TEMPEST compliance, which ensures electromagnetic shielding and security of sensitive communications, adds another layer of complexity. These chassis need to shield against electromagnetic emissions without compromising performance or functionality, which requires a deep understanding of electromagnetic interference (EMI) and precise material selection.
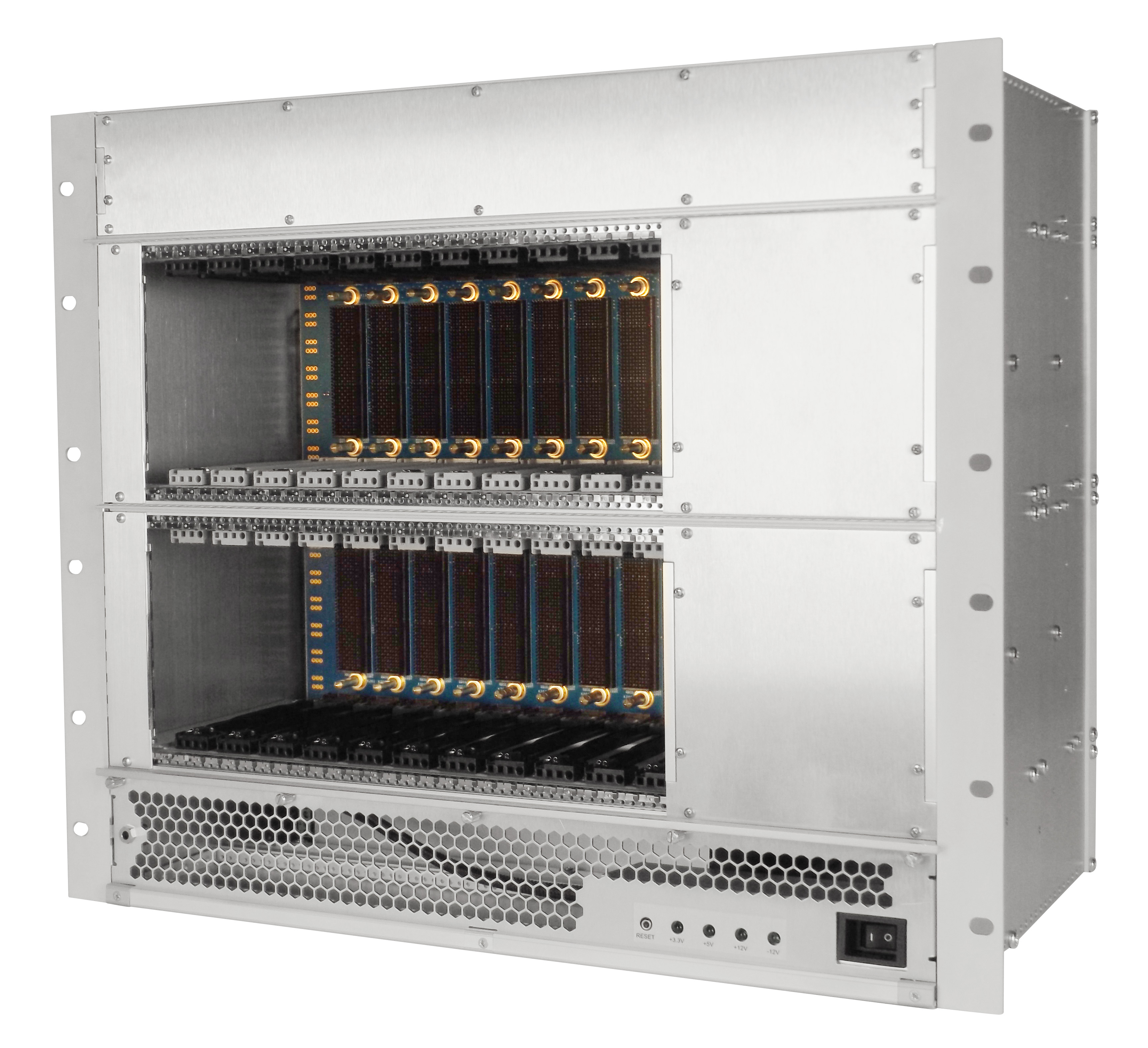
OEM & ODM Customization for Tailored Solutions
Custom OEM and ODM solutions are crucial when designing OpenVPX chassis for specialized applications. Each design must be tailored to meet the client’s unique requirements, which can range from military-grade toughness to industry-specific regulatory standards. The customization process is demanding, as it requires knowledge of the specific environmental stresses, form factor constraints, and military or aerospace regulations that need to be addressed. The need for customized solutions involves a precise balance between functionality, durability, and manufacturability, ensuring that every chassis is optimized for the specific operational needs.
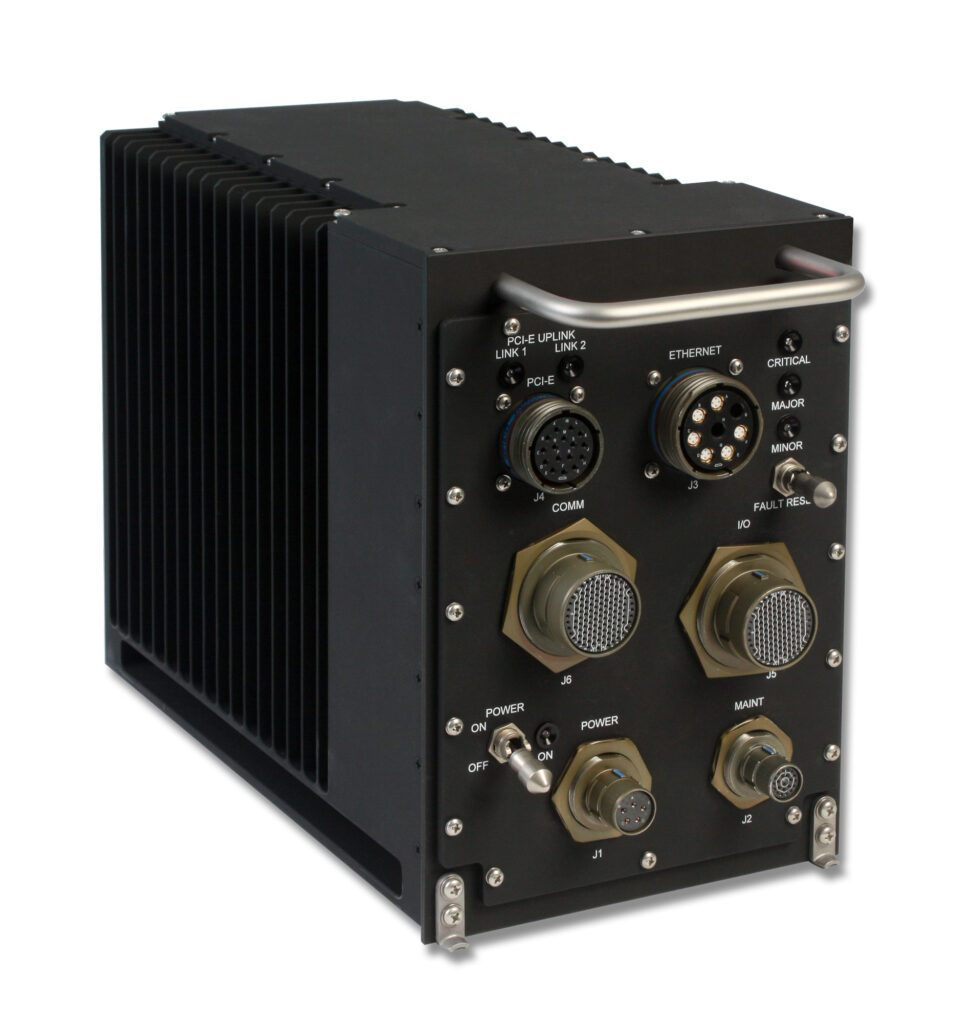
Development Challenges: Testing and Validation
The development and testing phase for ruggedized chassis is another critical and challenging aspect. Prototypes undergo extensive stress testing, including shock, vibration, and thermal tests, to ensure they can withstand the extreme conditions they will face in real-world operations. However, achieving the required balance between ruggedness and weight is a constant challenge, as military and aerospace applications often demand lighter enclosures without compromising on protection. Furthermore, the chassis must meet stringent military and industrial standards such as MIL-SPEC, which adds additional complexity to the design and manufacturing process.
Seamless Transition from Design to Production
Once the design is finalized, transitioning from prototyping to mass production involves ensuring that every chassis maintains the same high standards for durability and performance. This is especially challenging when producing small batches or custom orders, as quality control and consistent production standards must be maintained throughout the entire process.
Designing OpenVPX secured ruggedized chassis requires a deep understanding of the specific challenges faced by military, aerospace, and industrial environments. The process demands expertise in structural integrity, electromagnetic protection, thermal management, and precise customization to ensure each enclosure delivers the reliability and security required for mission-critical systems.